Mastering Preparedness: A Guide to Quality Control Inspections
Navigate quality control inspections confidently with expert preparation tips, from self-assessments to team training and documentation.
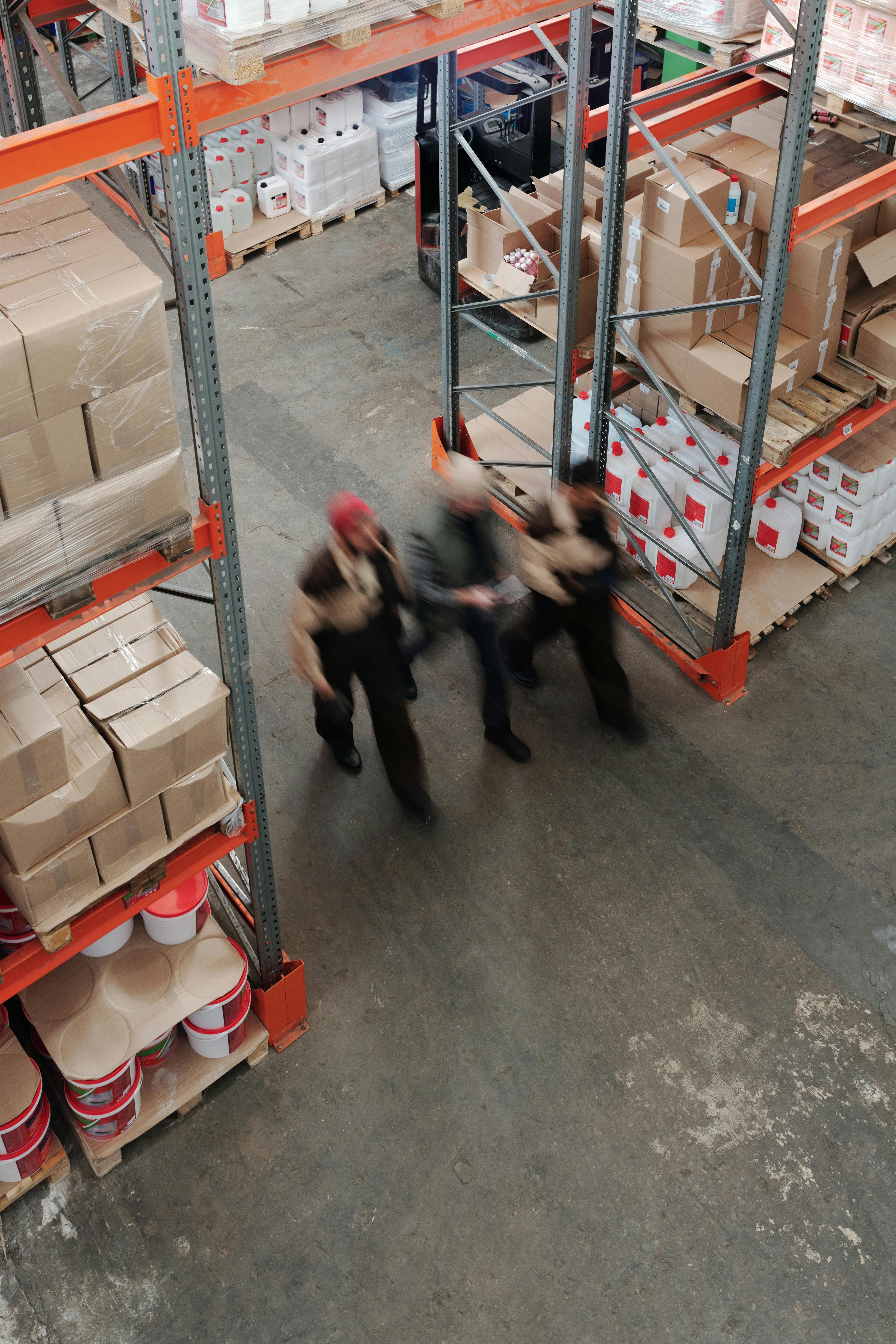
Understanding the Scope and Purpose of a Quality Control Inspection
Quality Control Inspections are pivotal in ensuring products and processes meet predefined standards of excellence. These evaluations safeguard the integrity of brands, fortify customer trust, and uphold industry benchmarks. By thoroughly assessing every facet of production and operation, inspectors identify discrepancies that could undermine quality, offering businesses the opportunity to rectify them before they escalate.
The focus areas of these inspections include but are not limited to material verification, process audits, and final product assessment. Inspectors utilize a comprehensive checklist that spans various quality parameters, ensuring every critical aspect undergoes scrutiny. Recognizing the inspection’s objectives demystifies the process, allowing companies to align their preparation efforts with the inspection's core aims effectively.
Conducting a Pre-Inspection Self-Assessment
A thorough self-assessment acts as the first line of defense in preparing for a forthcoming quality control inspection. This proactive approach entails a detailed internal review, mirroring the inspection process to unearth any potential quality gaps. By auditing procedures, products, and operational practices internally, businesses can identify discrepancies and implement corrective measures, minimizing the chances of non-compliance during the official inspection.
Steps for a Thorough Internal Review
Audit Against Standards: Employ the same standards and criteria the official inspection will use, examining your processes and products with a critical eye.
Identify Areas for Improvement: Highlight areas that fall short of standards or that could benefit from enhancement, focusing on high-priority issues first.
Implement Corrective Actions: Address identified gaps by revising procedures, retraining staff, or making necessary adjustments to product designs or compositions.
This preemptive analysis not only positions a company to better meet the inspection standards but also embeds a culture of continuous quality improvement, ensuring that high standards are a constant rather than a goal achieved in anticipation of inspection.
Aligning Documentation and Compliance Records
Ensuring your documentation and records are precise and readily available is crucial. These documents not only serve as evidence of compliance but also streamline the inspection process, making it efficient and straightforward. Maintaining up-to-date records, including Standard Operating Procedures (SOPs), training logs, quality control reports, and compliance certificates, minimizes discrepancies and expedites review processes.
Critical Documentation Management
Review and Update Records Regularly: Keep all documents current, reflecting any operational changes or process improvements.
Organize for Accessibility: Arrange documents systematically to facilitate easy retrieval during the inspection.
Such meticulous preparation demonstrates a commitment to quality and regulatory adherence, significantly influencing the inspection's outcome.
Engaging and Preparing Your Team
A well-informed and prepared team is essential for a successful quality control inspection. Employees should understand the process, know what to expect, and be capable of responding confidently to inquiries. Implementing training sessions that cover inspection procedures, quality standards, and best practices fosters a knowledgeable workforce.
Training for Confidence
Conduct Mock Inspections: Simulate inspection scenarios to give employees a practical understanding of how to navigate the process.
Clarify Roles and Responsibilities: Ensure every team member knows their role during the inspection, eliminating confusion and streamlining the process.
Empowering your staff in this way not only prepares them for the forthcoming inspection but also reinforces a culture of quality within your organization.
Ensuring Equipment and Environment Readiness
The operational condition of machinery and the physical environment plays a significant role in the inspection outcome. Inspectors evaluate equipment to ensure it is functioning correctly and calibrated as per industry standards. Additionally, maintaining a clean, organized, and safe workspace is equally important, as it reflects on your company’s commitment to quality and safety.
Maintaining High Standards
Regular Equipment Checks: Perform routine maintenance and calibration checks to ensure all equipment is in optimal condition.
Environmental Housekeeping: Implement cleanliness and safety protocols to maintain an inspection-ready facility at all times.
This proactive stance on equipment and environment readiness not only aids in passing the inspection but also contributes to the overall efficiency and safety of operations.
Establishing Clear Communication Channels with Inspectors
Open and transparent communication with inspectors lays the groundwork for a constructive inspection process. Engaging with the inspection team respectfully and cooperatively facilitates a more positive and productive inspection experience. Be prepared to provide requested information promptly and to discuss any findings openly, demonstrating your commitment to compliance and quality improvement.
Facilitating Constructive Dialogue
Prepare Questions and Clarifications: Anticipate areas where inspectors might seek more information and prepare clear, concise responses.
Maintaining open channels for feedback and post-inspection follow-ups ensures that you can address any issues promptly and effectively, cementing the foundation for continuous improvement and compliance. This level of preparedness not only smooths the inspection process but also positions your business as a proactive, quality-focused entity in the eyes of regulators and customers alike.